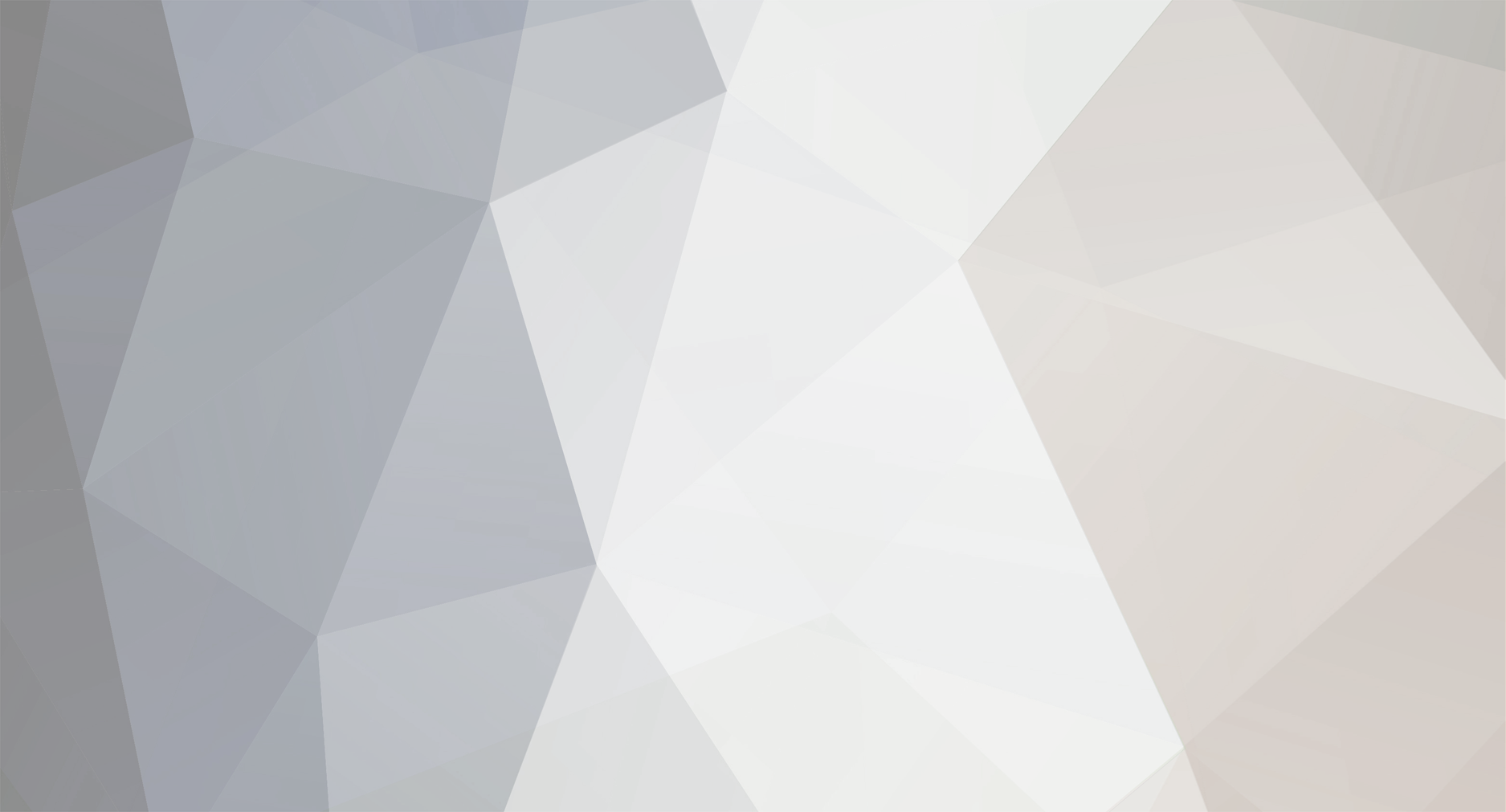
df8m1
Members-
Content
346 -
Joined
-
Last visited
-
Feedback
0%
Content Type
Profiles
Forums
Calendar
Dropzones
Gear
Articles
Fatalities
Stolen
Indoor
Help
Downloads
Gallery
Blogs
Store
Videos
Classifieds
Everything posted by df8m1
-
China?? I am in Michigan, USA. I have been developing Military cargo AAD systems for several years now, and will be developing a manned unit this year, so I am familiar with the requirements materials and such. I think most new jumpers have no idea about the annual servicing requirements when they are looking at making a purchase, they ask their instructors what they recommend, and then look for the best purchase price for that unit, not knowing that the recurring costs will add up over the life of the unit. Granted, they do not have many choices, so it really doesn’t matter I guess, as was said, it is the cost of insurance. Looking at it from a marketing stand point, one could either include the majority of the maintance costs in the initial purchase price, lowering the post purchase costs, or keep the initial cost lower, and then spread the balance over the life of the unit, like financing it. It is interesting to see that we have gone from, “it really doesn’t matter where it is made as long as it works”, to “nothing from China” lol. So it would seem to be more important that something not be made in China, than made in the USA,…. interesting.
-
I am wondering how many jumpers factor in the cost of the annual checks over the life of an AAD, and add that to the initial purchase price when they are shopping for an AAD?
-
[replyI'd be happy to see more options in the AAD market. I'll likely not select one purely based on price or location of manufacture. I may be in the minority but I have no issues with scheduled maint for these things. I think it's perfectly acceptable and can catch problems that a POST may or may not be able to. In the case of CYPRES I would like to see a longer lifetime. Agree with your comments on preferring a bottom mounted cutter for the reasons you identified. I'm not sure the market is saturated so much as there is (with good reason) trepidation with newer units. My current rig has a bottom mount cutter so I feel like I can accept more risk. If I had a rig that locates the cutter on top of the reserve I don’t have that luxury. An annual maintenance and a lifespan try to insure (as much as is possible), that the units in operation, are operating as designed, and to head off the eventual failure of the unit due to what ever. My TV was 4 years old and one day half the screen went black, the next day it was fine. Then two months later, half the screen went black again, and it was not that old. Circuit boards can crack, trances can crack from heating and cooling, solder joints can crack etc. I have repaired automotive electronics that stop working just by resoldering everything on the board. With a micro scope, if u know what you are looking for, you can see cracks in the solder that make an brake depending on temperature. Additionally, the baro transducers have a membrane that flexes as barometric pressure changes, and the data sheets usually will have a drift over time speck as the membrane ages and it’s flexibility changes. Now usually this drift is minimal, but it is possible to have some drift beyond the voltage reference’s ability to bring it back with in range when it is in for service, so it would have to be retired. Even the accelerometers can drift a bit over time and use. It is important to make sure all the instruments are indicating properly, because the software executes based on where it “thinks” it is.
-
I will attempt to approach this from a different direction using the above example as a reference. Unlike the above description of a manufacturer answering a question posted by a jumper, this thread began with an open ended question from a manufacturer to jumpers regarding an opinion based subject about, if there is a demand for an additional AAD on the market, and, if it being made in the USA would have any market advantage. This opens up to door to passionate points of view that can be considered as bias by others and to be blunt, start a pissing contest. There are Cypres people, and Vigil people, that will argue to the death that one is better than the other, or some such thing, I am pleased that has not been the case... yet any way lol. The idea of manufacturers answering specific questions is common sense, opening up a debate with the masses on the other hand has the potential for all kinds of issues, such as this argument it's self. No two people interpret information the same, and as such, there is always someone who gets their shorts in a bunch over something that has nothing really to do with anything, especially anything they are directly involved in. It is obvious that I worded my statement poorly, and that resulted in an unintentional interpretation that you are reacting to, and this undoubtedly could go on for years, and that, from my point of view, supports my statement regarding the possible risk involved in such a “taking of a chance” so to speak. In an effort to end this tangent, I will thank you for pointing out my poorly worded thought, you have avenged those of which I may have unintentionally impugned, and for that potential, I sincerely apologize.
-
Cypres is the name of a product made by Airtec GmbH - airtecjuergen - Juergen Sennert. They are third from the top of the list your so eloquently referenced, SSK is the USA service center for Airteck.
-
Once again reading the posts in the thread is alwys a good idea before posting.
-
I also thought this tread could be an experiment to see if it is possible for a manufacturer to communicate directly with the jumpers. I have been told several times not to try it, too risky they say. Are they correct?
-
yo mean Walmart?? I get a real rush looking at all the American flags in Walmart, with the little made in China tags on them NO. I watch the "Shark Tank," on TV other day,...And I was surprized to see that this show specializes in moving jobs offshore, just like MITT! I am tired to see companies move offshore, not good for our country. The problem is that no-one is going to switch AAD's, because a better, or even American Company makes it. Like comparing main canopies most individuals stick with just a few or stay with their first purchase. Which means your looking at the first time market, for the most part, tough market to penetrate, so to speak. Considering most startups want 80 percent margins and 100k take home in the envelope! Good Luck C ___________ This is turning into an interesting thread with two subjects emerging, pins and American's eagerness to send dollars over seas. I watch Shark Tank and Dragon’s Den too, I have learned a lot about how to approach investors and what they are looking for in opportunity and return. I would like to clarify, that I actually pay more for parts made in the USA, instead of having them made for less in China. I am not one to take a foreign made item and stamp a Made in the USA label on it. It is disheartening when I hear how casually people dismiss the significance of sending money over seas instead of supporting US companies in country. Regarding a properly designed cutter, to clarify, I am not suggesting a crutch for a poor cutter design, I am however looking at a potential failure mode given the cutter’s location, and the reported occasions that the cutter did not completely cut the loop. The challenge is really the loop material, as it is gummy. If it was brittle it would shier before it would smear so to speak, but the soft stretchy material that the loop is made from will squish and smear as apposed to sheering. From my understanding of the Cypres story, that they ended up having to design their own cutter because no one would make one for them. From my conversations with cutter manufacturers, they have a standard cutter design basically that they match with different charges to vary cutting force. These cutters are mainly designed around firmer cables, wires, or lines, so when you try to cut the softer, stretcher, loop material, sometimes the design does not have enough head room so to speak, and the line is not cut completely, or, portions of the line can get smeared and pinched between the piston and cylinder. Small variations in the loop material can have great affects on the cutters ability to cleanly cut the loop. I am trying very hard to not say one company’s design is better than the other, but rather discuses the considerations that relate to the process of cutting the loop. Every time I read in a thread the question, “did it cut the loop completely?” I get chills from the idea that someone’s reserve could have been locked shut, preventing the jumper from being able to deploy their reserve them selves. I had a couple of thoughts on a cutter that would remain passive, (allowing manual reserve deployment), in the event the loop was not completely cut, for what ever reason, (damage from packing power tools, loop material variation, or cutter design), that the jumper would still be able to manually deploy the reserve. Now, it could be argued that I am wasting my time addressing a non problem, and that’s fine.
-
Bent pins then, and pinched closing loops now, both are problems that can have an undesirable effect on the reserves ability to be deployed. Modern rigs have better reserve pin protection, but you are correct in that a bent pin can lock a reserve container just as a pinched closing loop can. In reality these are remote possibilities, but from my perspective, and I bet Mr. Cloth's as well, even small odds are too great, especially when you are the one speeding toward the planet. As you pointed out, Mr. Cloth saw a problem and set out to solve it, and in the original configuration, the cutter was placed on the bottom of the pack assembly, and this worked well until some long closing loops. (that if I remember right were not siliconed), took a set and prevented four reserves on the same dive from opening. As a result of that problem, the cutters were moved to the top of the pack, however, this solution introduces a new problem of the loop gets snagged or pinched in the cutter. Don’t misunderstand me to be declaring that cutters on top of the pilot chute are “Black Death”, or that one manufacturer or the other has bad cutters. I am simply looking at this from events that have taken place, and what possibly could. Like Mr. Cloth’s goal to overcome the bent pin potential, mine is to overcome / prevent the pinched loop potential.
-
[replyI always wondered if a system that actually 'pulled the pin' wouldn't be a better alternative...they way the old 'AOD's' were set up...? IMOP yes, pulling the pin as the only method of pack opening is the best, but the systems to do so are bulky compared to cutter systems. And with the modern tight rigs bulk is not a good selling point. For a student rig it would be fine, but those rigs are not stylish to begin with lol. Just moving the cutters to the top of the reserve had cosmetic affects. I have puller that I designed being used on a recoverable, sub orbital rocket, and I have concept designs of more compact pullers, but still the puller cable housing is bulky, then you add an RSL and the reserve rip cord has a bunch of crap on it which creates the possibility of other problems.
-
Yes, As I stated above, I do not like the possible failure mode where a pinched loop will lock the reserve up. Now it is obvious that the cutter is intended to always cut the loop and not pinch any of it, but I look at that as the glass half full. When the cutters were at the bottom of the loop, if it pinched, you still could save yourself, but with it now on top, if it pinches the loop the reserve is locked in the container.
-
Quote I would love to see more AAD competition. I've been waiting two years now for the M2 here in North America. reply] At the last PIA Alti-2 announced that they had the exclusive rights to M2 sales in the USA, but there is nothing on their site and M2 has a booth at PIA separate from them. Any idea what happened?
-
Of course it is not lol, a built in life span means potentially more future product sold, or the user goes with some one else with a longer span, or cheaper servicing perhaps. I have read all the patents for Cypres, Vigil, Argus, Astra, and some obscure ones as well, not worried about the electronic aspect, and my approach to the cutter is different as well, Sure I can figure that at least one will try to bankrupt me in an effort to keep competition from the market, but again, it would be interesting to know if Cypres went after Vigil, Argus, and Astra? I heard something about a cutter design or something years ago, but I do not remember who vs. who, and what it was over. All electronic AADs have baro pressure transducers and accelerometers, nothing novel in the use of those instruments there. Now the operational logic that uses the measurements is another story, and again my approach is / would be different. This is another financial risk that needs to be taken into consideration though. The whole purpose for producing a sport unit is to increase revenue, but compared to the Military purchasing volumes, the sport market is barely a sample purchase lol. Even if the sport sales were enough to cover the legal expenses, it would not be worth it. My investors have asked me a couple of times about a civilian unit, and each time I tell them the liability alone is too high, there is not enough gold at the end of that rainbow to make it worth while lol, and those thoughts are being confirmed. Really if you think about it, Sport Skydiving is a very small market, and only a portion of that market uses an AAD, so when you look at the two, or with M2, three, AAD manufacturers fighting over the small group within a small group, it is easy to justify not getting in the mix. Some times more money is made not doing something lol.
-
That is funny! Does it actually work?
-
The lawsuit aspect is indeed a factor, it would be interesting to know how much the AAD manufacturers spend each year for legal representation. I think Mr. Booth has the right idea with no insurance which is the big incentive for BS law suits. Perhaps it would be a better idea to create a shell company in Bermuda, I think that would help isolate the legal aspect, and would have tax benefits to boot! I can see producing something that sells for around a $800.00 / $1000.00 USD, (about 32% average less than a Cypres), if the volume were there (1000 + units a year), and I doubt that kind of volume is remotely achievable in the sport market given Cypres’s market share. There are some good reasons for requiring some kind of annual with this type of equipment, how often and how much it costs is debatable though. So far my personal thoughts have been confirmed, I thought I would throw it up in the air and see if it blue any ware. I can justify R & D on the cutter concept because it has Military applications, so if the fruit of that effort is sweet, it will be a matter of financial risk, and if it is worth it. I am surprised that someone has not come up with an App for a smart phone yet, then with a simple blue tooth power unit for the cutter, you could have an AAD that you can play Angry Birds on in the plane during the ride up, lol.
-
I am looking at this space currently as we, have / are, developing technology for specialized military applications that would transfer over to the sport applications with some tweaks. Even with a good portion of the instrumentation and processing logic proven or at a high confidence level, the capital outlay to design, build, and validate a prototype sport AAD is significant, let alone getting all the rig manufacturers to approve it etc, so regardless if it is a better AAD, with three or four AAD manufacturers competing for the small market, return on investment is a concern. I am confident that our operational logic will keep it from firing when you slam the trunk or car shut, or in the plane for that matter, and still initiate reserve deployment when it is set to. The issue that has been the back breaker for AADs is the cutter. I am not a fan of placing the cutter above the pilot chute for the simple fact that, if the loop gets pinched in the cutter, you can pull the reserve handle all day long nothing will come out. I understand why the cutters were moved from below the reserve, but I think a back up device should remain passive, always allowing deployment with pin extraction, even if the cutter fails to cut the loop. This is what I am currently looking at, and will be a vary large factor in my decision to enter this space with a product. The concept of performance being dominant in a purchasing decision is a good thing, a must IMOP, as, regardless of how much you spent on gear, being able walk back to the packing area is priceless. My curiosity is, given everything being equal performance wise, are there any pros or cons to where it is made, and would that influence your purchasing decision?
-
Full disclosure, I am Free Fall Accessories. With the exiting of the ARGUS AAD, again leaving only Cypres and Vigil AADs, (both made outside the USA), I am curious as to what everyone’s thoughts would be if an AAD was available that was made in the USA? It will be interesting to see how the M2 AAD does over the next couple years. As I understand it, the price is around (+-) $1000.00 USD, however it to is made outside the USA. Now of course I know that there have been AADs that were made in the USA, but they, for all intents and purposes, have faded in to history. I am asking, "what if you had the option of an AAD, (comparable in performance and options to current AADs), that was made in the USA?" Would you be more inclined to "buy American"?.
-
I am the head guy at Free Fall Accessories, Inc. I have been neglectful with the web site as I have been focused elsewhere. It is on the list of things to do, or more accurately, have done. I know I am probably walking close to the edge of the "no advertising" rule, so if I have crossed it, please edit it as you see fit, not that a moderator needs my permission Jump Safe
-
True air speed is not measured, it is calculated from Indicated Air Speed, taking into account Air Temperature and Humidity to determine the actual density of the air that is pushing against the sensor. Wind Speed has no affect on Air Speed, but it does change the Ground Speed. Taking GPS Ground Speed and Wind Speed to figure out what your Air Speed is, is not a good way to do it, as you pointed out. The first generation PFDR Pitot Static tube was designed based on a traditional Pitot Static Tube design, and keeping it level and straight forward was very important. That requirement is very manageable on a ridged aircraft, but a challenge on a squishy jumper. Additionally, it worked well with a square, but not at all with a round. The second generation Pitot Static Tube was designed using what I had learned from data recorded from the first one, the second generation Pitot Static Tube works as it should on both round and square canopies. Gathering consistent and accurate data that represents the actual, and ever changing, environment that a canopy creates, and or sees, is not easy. Additionally, with out experience in reading raw canopy flight data, it will be tuff to determine if what you are seeing is a true representation of the flight, or not. The first thing that the FS said when we analyzed some of the points during a flight is, “the canopy won’t do that”, but after looking at the other instruments that would have been affected, it was clear that “it can and did”.
-
The 'Trailing Bomb" is a simple unit that works well enough in straight and level flight, but does not work well in maneuvered flight, as, like a skier being pulled behind a boat, if the boat makes a sharp turn, the skier actually slows down a bit and then gets wiped to catch up, the Trailed sensor will do the same. I developed a Parachute Flight Data Recorder for the USDA Forest Service Smoke Jumpers, and a key requirement was an indicated air speed sensor. They jump special round canopies with a forward speed of about 10 to 12 MPH, it took two versions of pitot static tubes, that are mounted to the jumper, to make it work with a round and a square. If you want to know what the air speed is during a hook turn, (or a maneuver), then the Trailing unit will not be of much use, if you are interested in the speed after the turn, (where the Trailing sensor is again inline with flight) then that should give you a reasonable representation of the performance.
-
Does Consumer Reports ask permission of the companies to test their products? Does the IRS ask if they can audit you? Does the Insurance Institute for Highway Safety ask the manufactures before they crash test a car and publish the results? Did the federal government ask Toyota if they could investigate the latest problems (although I think in this case the politicians did it for other reasons).... 3rd parties doing testing without the manufacture helping is what keeps manufactures on their toes and challenges them to make newer, better, safer products and gives them the necessary fear of shortcomings being exposed. In any industry. Not saying we need it in our industry, but fair testing couldn't hurt.... (The problem with any testing is that the manufacturer's then design to the test, as in car manufactures making an exact replica of the crash test scenarios and perfecting their car, not to the real world issues, so in our case I hope the testing would be as close to real world as possible). I totally agree with what you are saying. That being said, I don't want to be that guy. I have too much personal respect for the manufacturers to assume that I know best how to test their equipment when I do not have access to the parameters in which the equipment was designed to, as there are two types of tests, tests to evaluate if the product is performing as it is designed to, and tests to evaluate how the product performs in a specific application. For example, if you preformed a design test with a 120 sqft reserve, it will pass, as it was tested using parameters that are scaled for a 120 sqft reserve. But if you tested that same 120 sqft reserve in an application with a terminal deployment and wing loading of 10 to 1, then the outcome may not be as positive. This is an extreme example, but perhaps another thing that needs to be decided upon is weather to test the design performance of the pilot chutes, or the application performance. Another view point is that a lack of design information would actually be an asset, as it would allow the tester to conduct tests without any influence of prejudice, (designing tests to achieve a preferred outcome based on knowledge of what types of tests would help make a particular manufacturers equipment look as good as possible). By not directly involving the manufacturers of the equipment that is being tested, it opens up the door for that manufacturer to dispute every aspect of the test as apposed to focusing on the results of the tests that they signed off on, and applying the knowledge to their product. Some ones equipment always comes up short, it is a reality that is unavoidable, and why I said, "Never ask a question you do not already know the answer too". We, the skydiving community, are a very small family, and I think that we should look after our own. Bringing in an external entity to conduct “independent tests” is asking for trouble IMO. Personally I think it would say a lot to the skydiving community and the wufos, if the manufacturers came together on this subject, and worked together in an effort to identify any possible improvements to, and or, set standards for reserve pilot chutes that could increase the chance that a jumper just has to buy a bottle and a case of bear instead of going for a well illuminated ride.
-
"The problem is there is no-one or organization that is going to conduct such a study. It's expensive and the results might be negative toward manufacturers." I was told about this thread by one of my partners, as I don't follow DZ.com much any more. He suggested that we offer to conduct a series of comparative tests, using custom data acquisition equipment we have designed for the USDA Forestry Service Smoke Jumpers, to measure and record parachute opening and flight characteristics for both main and reserve parachutes. Looking past the "pissing contest" aspects of the discussion, it does pose an intriguing challenge, and could result in new information that could increase the chance one of us walks away from a less than ideal reserve deployment situation. The first major problem that I thought of was, never ask a question that you don't already know the answer to. Speaking hypothetically, what if the data showed results that were not expected, regardless of whether it supports a positive or negative result? Either way it could like removing an air mattress from its box, it is easy to get it out, but once its out, you can never get it back in, regardless if it is the mattress you want to use or not. Same goes for ANY data, regardless of the validity, once it is out there you cant get it back in the box. I do not mean to imply that any manufacturer would prefer not to know if improvements could be made to their equipment, to the contrary, I believe each manufacturer would be very interested in any "conclusive" data collected that involved one of their products. The problem is the data being "conclusive" when the tests need to be conducted in the same non-controlled environment where the equipment is expected to perform. Wind tunnels are a convenient controlled environment, but the reserve system is not in a controlled wind tunnel when it is relied upon to save ones life, and it is in that environment that every jumper is interested in how their equipment will perform. It would take a lot of collaborative work to identify what specific equipment was to be tested, the scenarios in which it is to be tested, the design of each test, the evaluation process and standards to evaluate that the tests were conducted with in the parameters of the agreed upon scenario for each test, method of interfacing the data collection system with the gear as to have the least impact on the performance of the equipment being tested, and the interpretation of the collected data. Personally and professionally, I would never conduct any testing of any equipment without expressed consent from the manufacturer of the equipment being tested, and without their input and assistance in the testing process. It would be an interesting research project though.
-
We here at Free Fall Accessories, Inc apologize for the web sight status. We have been preparing a updated sight that will be launched soon. We would also like to thank everyone for there opinions and information regarding our Evolution Series mechanical altimeters. Our best advertising comes form our customers!!
-
This one was made for Bill Booth, honoring the 20th anniversary of tandem jumping. He E-Mailed me saying it is in his lobby and is part of the factory tour. Mr. Booth wanted a Brazilian Cherry Case to match the molding in his office. He also likes blue, so we use a blue Italian Velvet to cradle the Stainless and 24k gold altimeter. We made a different one for Ted Strong as well, To be shown later.
-
Very Nice!! You will most likely have to have someone airbrush your helmet. Dose your jump suit have a tail??