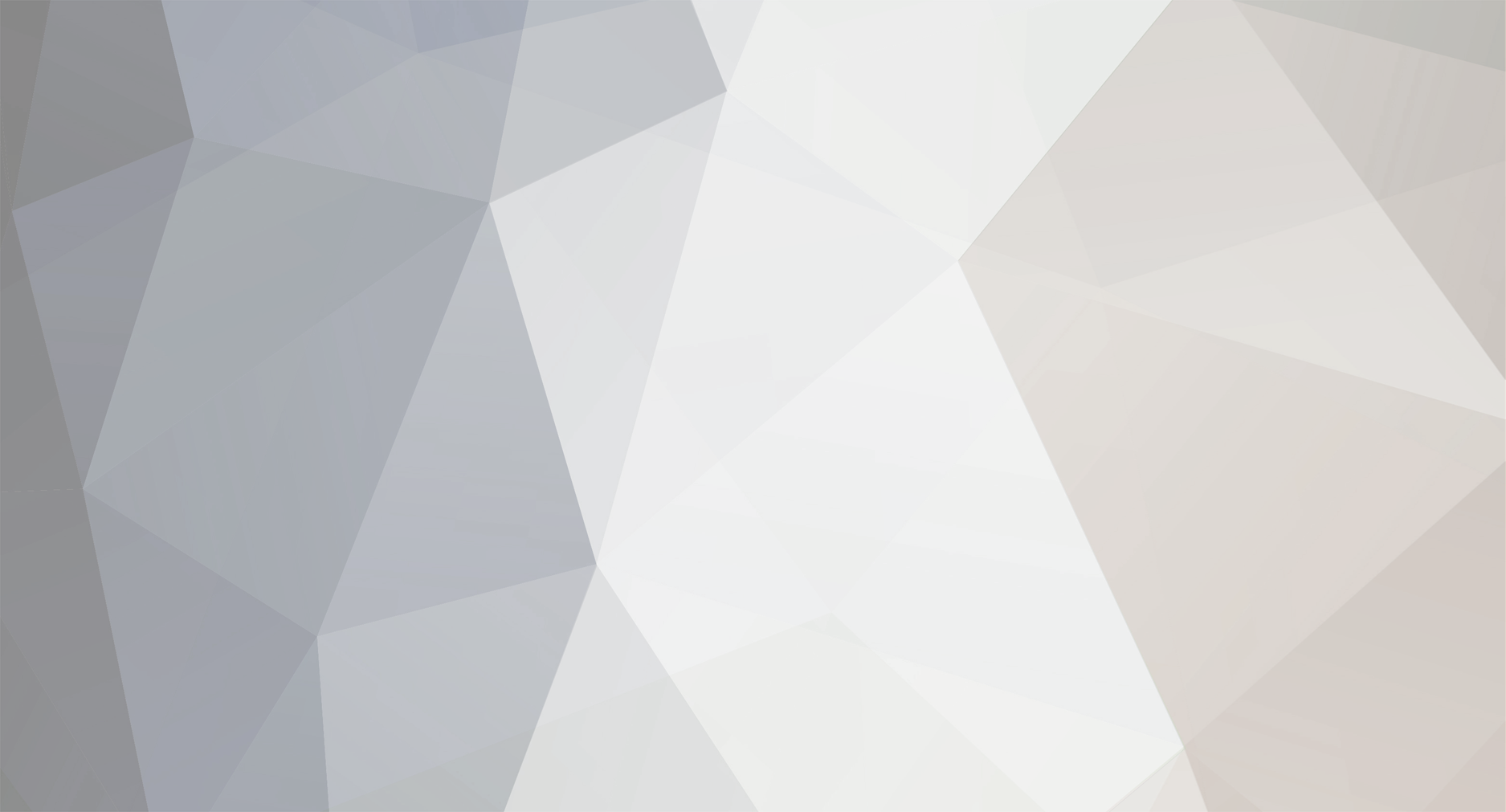
df8m1
Members-
Content
346 -
Joined
-
Last visited
-
Feedback
0%
Content Type
Profiles
Forums
Calendar
Dropzones
Gear
Articles
Fatalities
Stolen
Indoor
Help
Downloads
Gallery
Blogs
Store
Videos
Classifieds
Everything posted by df8m1
-
This is being done by PIA. I don't know the current status of the project. There are about 15 instances know and I have reports on most but frankly haven't even studied them in detail. No common factor to find. Remember tso standard is 3 seconds and up to.4. 300' if 3 seconds can't be meant for cutaways. 3 sec at terminal with firing alt. of 750 gives little toon for delay. 4 secs may put you in the dirt at terminal from 750' 750 was always the ragged edge but worked because most were faster when introduced. Now with new rig designs and reserves designed to be closer to 3 sec we've pushed into the dirt. That's why PIA risk management comm and others pushed for higher activation altitudes. For what little it's worth based on getting to know the principles I trust AirTec implicitly. I am neither a dealer or have other.affiliation with any gear other than a couple.of.pilot rig.manufacturers. LOL... Yeah... Someone mentions that every time there is a fatality... IMOP they are to closely associated with the manufacturers to do something like that without a cloud over it, if you know what I mean. I'm not saying that anyone would go out of the way to skew the results, but this is business and human nature. There could be a benefit from two or more methods to test as if the data matches (to with in a reasonable degree), then all is good, and if they are way off it would be interesting to see where the differences are and how the came to be. In other words, more than one effort would tend to keep all in check so to speak. I am very pleased that this has not turned into a specific manufacturer bashing or extreme defense of a manufacture thread, but the night is still young lol... As was correctly pointed out by another poster, there is a balance or compromise in order to avoid un wanted activations and still get them to activate when we need them to. There are several different ways to go about doing this, and the results can be seen with the history of the different AADs on the market. Also, as one poster pointed out, there are several instances of reserve pilot chutes in tow, which scares me almost as much as a broken pin. My rigger checks how much it takes to remove the free bag from all of my rigs, and not because I ask him to. I was thinking today that there could be several issues, each alone being deadly, and each occurring very rarely so to speak. So as was pointed out, if it appeared that a manufacturer was to “hypothetically” make a change to their design in order to help avoid a “hypothetical” equipment malfunction, then it could appear that the manufacturer was admitting guilt. But, if they all pointed their fingers at each other, and in the mean time, raised the min reserve deployment up a little as a overall good idea that in no way is to imply that there is a problem, but rather just good regulation, then after a while it will be forgotten. That’s my conspiracy theory for today lol.. Personally I think that 750 ft is too low for a last ditch reserve effort, I do like 1000 ft better. (NOW I’m not saying I agree with the higher main pack opening altitude, just a higher reserve opening altitude) You can’t bring back the dead, so as long as another jumper does not go in after an AAD fire, or if they pulled the handle at an appropriate altitude, then all is good. BUT… That being said, I personally think that we owe it to our fallen brothers and sisters, as well as their loved ones to find out what happened, even if that means they screwed up, which I bet would be more the rule. It is when the jumper did everything right that I am really interested in. Yes, a jumper should not put their life in the hands of an AAD, but, if they are going to take that extra step, and add an AAD to their gear, then the chose of which AAD to buy “could” be the difference between life and death, or at least it appears that may be the case, and the same may be the case for container and reserve combinations as well. I hope I am not coming off as a finger pointer, or looking to cause trouble as that is not the case. We as jumpers have been allowed the freedom to self regulate, and IMOP we have done a piss poor job of it. I think that this type of problem can be handled internally with out tremendous fan fair if everyone is open to look into the deep dark corners of each instances regardless of what implications may be drawn , weather proven actual or not. Certainly a test standard for AADs is a must. This could be simply a standard method of confirming that the AAD performs as the manufacturer says it will. As long as “it does what they say it will”, with in a reasonable tolerance, (to be determined by we the people), then all is good. And when there is an incident, the gear, all of it, undergoes this standard test, and its performance is evaluated independent of the manufactures. This way each AAD manufacturer has the freedom to have their AAD perform as they like, as in, activate 10 ft above the ground, as long as it’s performance is confirmed, then it is up to the consumer to decide if they like that performance feature in their AAD. And I too like the idea of having a log of what exactly was done to an AAD throughout its life, this is a requirement for an airplane is it not. It would be interesting to know exactly why some AADs have to go back to the factory.. this would imply replacement of parts, as software is easy enough to down load is it not? A log would provide a history that could hold valuable information in a fatality investigation.
-
Absolutely, that data would be very valuable, but to more than just jumpers, the layers would be all over that as well. Something happened to both jumpers equipment that caused them both to fail to operate with in any of the manufacturer’s specks. I know that is another bold statement, but it is not like they both were using the exact same container, container size, or reserve size. I’m not even sure if both reserves were of the same manufacture.. Now one could argue that one can not make any speculative statements given that one does not have all the facts, but none of us do, that is, none of the actual people who chose to expose themselves to great risk based on the trust / belief that their equipment meets, and will perform at, the basic requirements, (provided that it has been maintained and was operated with in the parameters accepted by the manufacturers, i.e., if the reserve fails to open because it was activated too late, then it is not the reserves fault as it did not have enough vertical distance to operate with in the manufactures speck). It is up to us as jumpers to save our selves, that includes post incident, arm chare, investigation, in the absence of anything else.. But isn't the idea that the capacitor is always charged up, so that a higher current discharge is available extremely quickly to fire the cutter? The extra battery thing in the Vigil is sort of a hybrid battery / capacitor. One statement on the web about them: "Pulses Plus™ batteries were developed at Tadiran and introduced into the market few years ago. These batteries combine a primary high-energy bobbin type Li/SOCl2 cell with a hybrid layer capacitor (HLC). The HLC is a battery-like capacitor consisting of lithium intercalation compounds as electrodes with pseudo capacitance of 785F for standard AA size". But what does the Cypres use? From opening up the Cypres 1, there is no big capacitor in there. My photos show only what look like a couple small ones on the circuit board, no more than 1 cm long and 1/2 cm dia. Whatever their design, it normally seems to work. The batteries used in AADs are generally made to put out a small about of currant over a vary long period of time, as apposed to a car battery that is made to put out a lager amount of currant for a short period of time. The pulse battery you mentioned is just like a car battery, it is made to put out a lot of power for a short period of time, so it is great for firing a cutter, but would not be good in your walk man.. Super Caps are used to fire cutters and they are most commonly available in flat wafer type design. This makes them great for stacked circuit boards as they are thin, but have a larger foot print. The main benefit of using a capacitor to fire the cutter is that a slow discharge battery can be used for the AAD, and the cap is slowly (relatively speaking) charged as to not collapse the battery voltage by drawing too much power. Once the Cap has been charged, then it can discharge a lot of power very quickly. It is not uncommon to also boost the cutter voltage to a higher voltage than battery voltage which reduces the amount of currant required to fire the cutter. There is a balance between battery output capacity, boost regulator output, and capacitor size. It is a waste of battery power to charge the cap every time the AAD is turned on, so when they are used, they generally are not charged until the conditions closely approach firing conditions. I do not know if the Cypres 1 or 2 use a cap, if they do not use one, then the required charge time is taken out of the equation. Electronics are funny in that we can not see what is going on in there.. The more I work with electronics and code, the more I am amazed that it works lol.. then again... I have seen the same code in 10 prototypes and some work fine and some have problems that pop us once in a while..
-
The answer is neither. It is a jumper problem. While interesting, I think you are embarking on an exercise in futility. Unless you can pinpoint absolutely a problem with the AAD itself, the variables are just too great, because the circumstances of no two incidents would ever be exactly the same. In the end everyone must understand that an AAD is a backup device, and nothing is guaranteed when margins of survival left by the jumper are left so slim. At that point it is either your lucky day......or not. This is a good point. Too many jumpers these days put way to much responsibility on the AAD to save them instead of them selves. Additionally, the general lack of equipment working knowledge puts them at even more or a disadvantage so to speak. I design and build parachute data collection systems and have discussed developing a process to measure every critical aspect of the rig and reserve. One way to look at it is, it is business.. I often am told that there is video of everything happening and they know how long it takes for X to happen, but I then say, how much force was the pilot chute generating behind the jumper during that test? How long did it take from when the pin was extracted to when the pilot cute left the container, or when the free bag left the container? This is something that John Sherman has been talking about in regards to using a shorter bridle to save some time, but what does that do how much pull force the pilot chute can generate in the burble behind the jumper? If there was a standard test method then next time there is an incident, the gear could be tested, granted it is not as simple as that, no, not even close.. What I have struggled with is, what if there is a combination of equipment that in certain conditions fails to operate with in TSO standards? Then what?? As I told one of my partners, “you can’t put the shit back in the horse”. And at the same time, given that this could be done, to, at the very least, allow us as jumpers to say that we have done everything that we can do to keep this from happening again, would it not be prudent? Just as Consumer Reports does independent crash tests, that the OEMs always contest, unless it makes them look good that is.. There is a lot of politics involved, as well as several different countries, languages, and cultures with such a project, which can make it difficult if one whishes to involve the manufacturers in the process. But back to your thought, I agree that it is the jumper who is ultimately responsible for saving their own life, so long as their equipment will allow them to do that.
-
Good to know they both had the same AAD. I also believe the other instance I seem to recall was a Cypres as well. Please do not misinterpret any mention of a specific AAD as bashing them. Just looking for commonality in equipment and what happened. So that takes the "turned it on at home" possibility off the table in this case. Every electronic AAD is supposed to adjust for barometric pressure changes throughout the day, and I think that all the electronic AADs will fire at a min of 750 AGL. That is if it is working and calibrated properly. I cant imagine that the student rig was a tight little one with one of those new reserves that is said to possibly take more time. If the instructor had a perfect storm so to speak of tight reserve container, and slow reserve, (not saying it is or isn't.. I have not measured it yet), then I would have not thought twice about it if the instructor went in and the student's reserve deployment was as other AAD deployed reserves generally are. But in this case they both went in wearing two different container and canopy combinations and both with the same AAD. Both individually rigged jumpers hit the ground before either reserve could inflate. The Cypres 1 used an analog pressure transducer and I have not had a Cypres 2 apart to know if they went digital or stayed with the Analog, both have pluses and minuses. One would think that the sensor would put out a steady reading if it is on the ground, but they do not, there is always noise to contend with. The sensors are actually very close to the bottom of their scale when at sea level. I have used both Analog and Digital baro transducers and neither will put out a solid number without a lot of averaging. If the sensors in both AADs were part of the same batch, and that batch of sensors was noisy, or became noisy after some use, (I have had to reject a batch of sensors for that reason),(remember every 4 years they have to be checked, and some have to be sent to the manufacturer, and there was a batch of them recently that had issues with a component, Again I’m not bashing the Cypres). It would be nice to know when both AADs were made and their service history. The noise is a ranging output frequency and the actual location is some where in the middle usually. If the noise band is wider then the program is ready to handle, then the gradual changes in ground level barometric pressure could easily be lost in the noise and not compensated for. With out knowing what every jumper was using, how it was maintained, and the conditions they were jumping in, it is almost impossible to find a thread of commonality gear wise, let alone the conditions. This case offers a little more potential as there were two different rigs in the same conditions, and both jumpers died from impact with out an open reserve after an AAD deployment. The only difference between the two jumpers deployment processes is I think the instructor had pulled his reserve handle, and I do not know if his loop was cut or not, but both AADs reportedly had fired.
-
One of the projects I am working on is instrumenting up a rig to measure reserve deployment sequence times, vertical distances, and forces. A thought occurred to me the other day while thinking about jumpers impacting with the reserve at line stretch after an AAD fire. As far as I can recall there have been at least three instances, I may be incorrect on the exact number, but in one case it happened to two jumpers at the same time. Both AADs had fired and neither reserve was useful in time. It is that instance that really shakes up the argument of if it is a rig & reserve problem or an AAD activation problem, as they were two different rigs, and I do not think they had one of the reserves that may or may not tend to open slower than it should, as in, require more vertical distance to arrest the jumpers descent rate to a survivable one. Although I do not think that the type of AAD in either rig was identified, that would be the only thing that two different rigs could have common which would have an influence on reserve deployment initiated by an AAD, other than possibly a common rigger with very bad rigging practices, which is not impossible. The fall rate of the two jumpers was higher than that of a stable neutral body positioned jumper as one was tumbling and the other was in pursuit (student and instructor), which could have an affect on the actual activation altitude depending on the firing protocol of the AAD. If a capacitor has to be charged prior to firing, then that takes time, and if the jumpers are falling faster then the vertical distance fallen will be grater during the time it takes to charge the capacitor. I have seen and heard of head down jumpers being saved by AAD, so if the fall rate is a factor, then perhaps their AADs were not working as fast as the majority of the other AADs?? But two AADs having that same obscure problem at the exact same time??, I guess anything is possible.. I am thinking that a more likely reason that both AADs would fire too deep (at the same time), would be that they, the AADs, were not adjusting the AGL altitude as the barometric pressure changed during the day. Even if they turned on the AADs at a lower elevation and then drove to the DZ, unless they immediately jumped on the plane, the AADs should have adjusted for the new “zero” after a period of time at the new elevation. That is why it is not good to fly at a constant low altitude for very long. I would love to see the barometric pressure readings in that area during that day. If the pressure gradually drops throughout the day, and the AADs did not correct their “zero” then they will think they are higher above the ground than they really are during free fall, and the onboard data would indicate that the AAD fired at the proper AGL altitude. We zero our altimeters every jump before we get on the plane, how do we know that our AAD has also made the adjustment? It is not uncommon for the barometric pressure to swing + - 250ft during a nice weather day. Again both AADs would have had to fail to make the proper pressure correction, but then again, why do service centers have to send some AADs back to the factory?? The good news is, now that the AAD firing altitude is starting to be accepted at a higher altitude there is more room for error in regards to fall rate and “zero”. Full disclosure, although I do not make a civilian AAD, I am designing military AADs, and I think I am going to have them indicate when they make a zero correction and how much it was. It would be nice to be able to track it with my altimeter. Personally I do not agree with the “set it and forget it” philosophy or set it and trust that it is doing what it is supposed to do for that matter, I am more of a “trust but verify” kind of guy. Again, just a thought, I don’t think that this possibility was ever discussed while those incidents were in the forefront.
-
Yeah until their lawyers find out what you are using it for lol..
-
Positive thoughts your way! lol Customs can be a PIA some times. Do you have the Customs Declaration number? You can use that to see where it was last processed, and get an idea of where it is in the system.
-
There are always plusses and minuses to everything lol... I have looked at making something several times, but every time I just don't see the monetary incentive to develop something to a level that I would want. Even compared to $2K for a new canopy, that is cheaper than what my investment would be to make something cost effective while performing how I want it to.. I am really curious to see how this turns out.. I mean it turns on during a jump and then off after a while of in activity unless it has been pinged, in which case it would remain on if it's operation requires it.
-
Seeing how accurate it is, is not a big deal. Just have someone go off some where that it would be hard to find a canopy and see if you can find them..
-
Are you approaching this from a personal perspective (one for yourself), or do you have a marketable solution in your sights?
-
As has been stated before, there are several options that are tailored for other applications that if integrated properly, could serve very well for canopy or even rig recovery. The issue is the integration into our equipment.. Addressing all the little details that make a product attractive to a user is costly. I have quite an extensive file on this type of product, but I still do not think the market would make it worth my while, and I am sure that I am not the only person/company to think that because not one has moved on this "opportunity?" lol Something could be rigged up quick and dirty by an individual for him/her self, but to refine it to a marketable level will take some investment..
-
Any Updates? I am curious as to how excited the container manufacturers are after the last youtube test?
-
As if there are not enough twists and turns with this already... a thought accrued to me and I debated if I should share it or not... it is based on a physiological analysis of the situation as a hole, not a technical argument… Keep this in mind… Let me start by saying that John is very intelligent… and seems to have a flair for the dramatic lol… Any way… My point is he is not in any way lacking the gray matter to putt all the pieces of the puzzle together regarding what it would take to make his rip cord a truly viable option, that history alone would determine if it was the revolutionary contribution that I am sure he wants it to be. So what if he never had any real intention of this being furthered to a state where it could actually compete with the other options that he so admittedly lobbies against, and potentially be rejected, or, go to the wayside like all the other pin pullers that have come an gone during the evolution of gear? What if he is just board sitting at home in his bathrobe, and this gives him an opportunity to get out of the house, remind himself of a time that once was, and stir up the pot, all the while carefully positioning himself at a point where it will take action from others to further the process?? (Action that is very unlikely and he knows that, remember he is not dumb)… This would allow him to say that he has the solution, and he has done all he can do to save the sport from the evil cutters, but, because of the lack of understanding of the industry, everyone with a cutter will still be at risk and illegal... If the rip cord is never put into the field, where any short comings will show up over time, as they have with the different cutter designs, then it will forever remain pure and untarnished legacy …. Again… This is just a scenario that has played out in my head as I try to follow the logic of presenting half of a device… All in jest, but is it possiable??
-
Fair enough. But given that you've talked with Karel, is the rule about changing the battery at every repack total B.S.? Or is is the electronics design so crappy that its going to drain the battery in 180 days and fail to power up or fire? That rule was added in near the end of the time where the AAD was fully supported, and it wasn't clear to me whether it really was a problem with the Argus, or it was something that Karel did while flailing around trying to save the situation after all the bad press about cutters. After all, the rule is worded so that even if a jumper has a cutaway the day after a repack, he has to have new batteries again put in the Argus. Sounds like a rule made by a man who wasn't thinking. It really leaves open only 2 possible answers: a) the electronics are terrible for this day and age, or b) it is a useless rule imposed on users by a desperate company, a rule that continues to cost jumpers using the Argus AAD. I do wonder whether that rule is really needed or not. But with that rule being there, I do follow it for my rigging customers. P.M. me if you'd like me to start a new thread to address that issue, if there's a lot you can say about it. I intentionally did not ask for or about any specific operational specks, (because I did not want to risk any problems given I am designing my own units), other than the firing circuit as I was considering making a cutter that was compatible with it, so as to your question regarding the possible relationship between the battery change intervals and the power efficiency of the design, I do not have any knowledge on that, even if I could talk about it. Speaking from the perspective of an AAD manufacture, I could imagine that given the batteries were "off the shelf" there is no way to control the quality of the batteries used or their age. The overall capacity of the 1/3 A batteries that are used is not nearly as large as the Cypres for example, so that might be a reason for the preventive measure, (smaller capacity and uncontrollable quality)?... The Argus has a low battery warning feature that will indicate that the batteries are at a low capacity level…so as to why the change in the battery replacement schedule, I do not know.
-
I have spoken with Karel several times during the period that I was considering making a cutter for, and then possibly taking on the Argus, and I we have a NDA in place which I have to be mindful of when speaking of the Argus... I like Karel, he is a very passionate person, and that passion that has, at times, not been great marketing or PR lol... He and I talked about how the problem was handled, and agreed that it could have been done better, but that is water under the bridge... At the same time period, Aviacom and PIA were at odds and I think Karels interest in pursuing a third generation cutter was lost... Personally from what I have seen, I think the Argus controller is as solid as the others on the market, and given the fact that there are still Argus units in the air, and we have not heard anything negative about them, tells me that with a proper cutter or actuation device attached to it, that the Argus AAD could make a comeback. We received a lot of support from people and manufacturers at Daytona when we were considering the Argus.. I think John would be served well if he decided to go that route..
-
I can't speak for Cypres or Vigil, but I am working closely with the company that will be making the pyro initiators that I will be using with my cutters. Quality assurance is the end all be all of it, plus in my case there are some government requirements that the pyro manufacturer needs to be able to meet.. I designed my firing circuit around the specks that they have provided, and will have them do a firing confidence study to insure that everything is compatible with some margin of head room. Do the AAD manufacturers make the cutters that they designed their AADs around, no, do/should the AAD manufacturers work closely with their cutter manufacturers to insure that the cutters that they make consistently meet stringent quality requirements, throughout the entire assembly process of the cutter...yes.. With a cutter, when it leaves the factory, it is assembled, no further attention is required outside of a quality controlled system... With the rip cord, some one out side the quality system, (argued to not even be required to be a rigger by the manufacturer of the rip cord), has to assemble the thing and install it properly. I imagine if the housing and ripcord are not positioned properly that the piston could be out of the short cylinder or barely in it... What if like Lee said, that the housing was not tacked down good enough and there was a really hard pull which caused the housing to move and not the rip cord??... What if there was a problem with the connector where it had a good enough connection to pass the cutter detect, but was not up to the task of carrying the current required to fire?? This would be another in the plus coulomb for the Micro Puller as it would be a self contained device, requiring no assembly out side the factory, the Rigger just has to slide the pin through it and route the wire properly. When some one hammers in, one of the first things that is asked is, "did they have an AAD?" and then it is "which AAD did they have?"... If anything in the system fails, the AAD is not going to work, and their name tied to a bounced jumper is just bad marketing.. Now should an AAD manufacturer decide that it was worth it to them to invest the money to properly test the compatibility of the two devices, and invest in a proper, quality controlled production facility, where in the rip cords are installed, then that might make sense to the AAD manufacturer share holders.. Given that the Cypres was created because of a pin, I think I am safe in saying that they are out... Maybe Vigil ??.. The Argus is the best option for this, or if John designs his own AAD to go with it.. Time will tell if the container manufacturers get on board as well as the AAD manufacturers... "Nothing is impossible, no matter how impractical, so as there is sufficient funding to peruse it." DLW
-
I agree, and could make them, but again.. with out an AAD to activate them, it would be in the same situation as the ripcord, only it would have different arguing points. The idea that an AAD manufacturer would approve of a device that they have no quality control over, and have not done the testing of the combination, (expensive to do), to see if there will be any problems with static or EMF, is more of a dream IMOP... The main marketing angle that the AAD companies have is reliability of the "system".. I guess they would still be able to say that the control unit would be reliable, that is if they had done compatibility testing first... And by them accepting anything than their cutter, I would think the roomers that there was a problem with their cutters would start... Edit: Now that there are a couple of videos showing it working in ideal conditions, (no real surprise there), I would like to see another set of videos showing it working in not ideal conditions, such as, a with a bent pin that requires, say at least 50 ish lbs of pull force, (or more if he really wants to get friskily) to start the pin moving, of course a verification of the initial pull force would need to be videoed (not a full extraction, just a standard post pack job pull force test to set a base line). Additionally good videoed inspection of the housing prior to, and after the firing, would be good to show if the housing moved due to the higher pull load.. My understanding is that the Cypres is around today because of a bent pin, I have seen them my self, and regardless of the “likely hood of” argument, they can and have happened with fatal results.. So.. in order for “any” pin puller to be argued as “a better option” than a cutter, this failure mode must be overcome consistently…. Realistically it needs to work regardless of how badly the pin is bent, as a good cutter will/can open a reserve with a pin that is bend 90 degrees, or with a broken pin..
-
It may very well come down to Parachute Labs having to install every one that they sell and take the liability for all that a jury might assign. There are lots of riggers that will pack a reserve for $70.00 and there is risk in that if they do not do what they are supposed to, but how much could they charge for installing a power ripcord, given the liability they “may” be assuming?? The reserve will need to be resealed after install, and personally I would never put my seal on someone else’s pack job (again I am not a rigger), so that would mean that the install would require a pack job as well, (which is not a big deal at the 180 day mark). Even if the manufacturer approves of this mod, there is still the issue of plugging a aftermarket device into an AAD of different manufacture. What technical documentation would the rigger have supporting the compatibility of the two items? So the AAD sees the igniter… OK… how about how the AAD’s firing circuit handles static? Or EMF?... These are things that each AAD manufacturer had to deal with when they designed there AAD and their cutter was part of that design, not this ripcord which could act as an antenna, or lightening rod… Now I am sure that both John and Karel are screaming at the screen that I do not have a freaking clue about what I am talking about, but even if that is the case, neither will a jury… That is the main reason I will not produce a civilian AAD is because the jury has no idea about the skydiving world besides we are all reckless daredevils with a death wish, and manufacturers are exploiting that for profit.. When AADs first came out, you could say that the rigger that installed them was assuming all the risk, but as long as it was approved by the container manufacturer, and the rigger installed it per both manufacturer’s specks, then he should be good. In this case, even if the container manufacture is on board, you still need the AAD manufacturer’s blessing to maintain the same level of liability. I do not see any AAD manufacturer endorsing an aftermarket device as when someone goes in, their name will be part of the discussion, and that is not good for business. It just makes the most sense for John to take the Argus from Karel and offer a complete package so it can stand on it’s own.. He is already promoting Karel’s idea for the ripcord, so why not put his AAD behind it and see if it sells?
-
My thoughts were more toward the legal angle, but they are why I personally prefer a good cutter as a secondary method of pack opening. If a cutter is bad because it “could” or “has the potential to” prevent the reserve from deploying (when located above the reserve), when the jumper wants it to open, then why would any other component that plays a role in the deployment not be equally evil? For example, if the pin brakes, (we know that has happened, the service bulletin and all), the reserve will not open when the jumper wants it to, just like a pinched cutter that is above the reserve. If the pin is bent, it “could” create a hard pull that “could” prevent the jumper from pulling the pin, which would prevent the reserve from deploying when the jumper wants it to, just like a pinched cutter that is above the reserve. If the ripcord cable is jammed in the housing, that “could” result in a hard pull that prevents the jumper from extracting the pin, which prevents the reserve from deploying when the jumper wants it to, just like a pinched cutter that is above the reserve. Moving on to the next critical link in the deployment chain. Lets say the pin is cool, but the pilot chute spring is broken in pieces… That “could” prevent the reserve from deploying per the TSO standards, potentially not as bad and not having the reserve locked in the container, but definitely not desirable. Or if the spring fatigues and takes a set, (looses the majority of it’s tension) that also would have an effect on the reserve deployment… My point is that singeing out the cutter as the “only” part that “can” be in violation of a TSO, “as in it could negatively affect the reserves ability to deploy within the TSO requirements”, (should it malfunction), is short sighted, and leans toward a marketing perspective IMOP. If the pin or the spring screw up, regardless of the likelihood of it happening, which is not a factor in the argument, (we are talking about items that have the “potential to”, not the ”chances of” or “likely hood of”), the end result will/could be the same as a pinched cutter that is “above” the reserve, and there for, are/should be, subject to the same stigma that the cutter is being given. Changing out a ripcord and housing set that is loose, (the cable will freely move back and forth), with one that has the cable tight in a cylinder, with seals and all that could stick to the pin or cable and be pulled into the housing jamming it, would present a new opportunity for the reserve to not deploy when the jumper wants it to… Regardless or the “odds of” it is the “potential to” that caries the weight here. It is the design of the item in question that determines the “potential to”, as well as the “odds of”. If the potential is there, regardless of the “odds of” then it needs to be acknowledged. Consider it full disclosure. I understand that there is a desire to sell more ripcords here, but lets keep the big picture in focus.
-
I do think that some installations of certain containers are susceptible to container lock if cutter does not sever the loop. Others not so much (like the Javelin placement on bottom - which I like) That said, If its an approved installation as per container and AAD manufacturers guidelines I think you may have some defence. That said I prefer installations which don't have the potential to cause container lock in the event of a fail cut. This pin puller /pusher is a different solution and perhaps has less inherent risk as it always allows manual activation. Just thinking out loud here, but if cutters are evil because they have the potential to lock the reserve in the container, than how about a bent pin that prevents extraction?... or a cable that is jammed in the housing from that landing in the pees and cant be pulled?... or what about a broken pin??...That one makes me sweat just thinking about it... Having a close toleranced piston and cylinder assembly that is crimped to the cable has the potential of jamming and preventing a pull... or is a broken, bent, or jammed pin not illegal because the flaps never opened?? The reserve is just as locked in the container as it would be with a pinched loop in a cutter, but this is OK?
-
I’m here to help!! LOL…..But seriously.... Like I said before, being challenged is a good thing, never a bad thing, and you have chosen to look into the challenges and see what there may or may not be about it. Good for you. Like I also said, if you can not answer a challenge, there is a problem. Have you given any thought to taking the Argus and offering a complete AAD? I’m sure you have, but I am wondering what your thoughts are about it. I took a serious look at it, but in the end I am building my own units that operate completely different, and it would take a redesign to get the Argus to do what I want, plus the liability of the sport market. But, you on the other hand have ½ of the system, and the Argus would be the other half… Edit: Just another helpful hint from the peanut gallery... It would be nice to see what the pull force measurement is on the rip cord each time, before you fire the power unit.
-
I couldn't make it zoom in when I looked at it, so I could not clearly see the time scale, that sounds shorter than I would like personally. Could you tell if the piston was able to move or not? I know you asked about the leakage rate earlier. Personally I would want to see it hold working pressure to generate at least 50lbs of pull for a period of at least 3 sec to show that it was sealed reasonably well. Realistically from activation altitude there is only a second or two to play with for pack opening, but I would expect to see full power available at the pin to get et moving at the for at least a second, and then drop at a rate equal to the piston displacement and any cooling of the gas. I am sure John really loves us right now lol..
-
John and I talked about this in Daytona and I expressed concern where John dismissed it. Personally if I was a rigger (which I am not) I would not touch a rig with any Frankenstein assemblies that in any way related with the reserve, for the very reason that all manufacturers will be blaming the other and they have better legal representation that the average rigger does I imagine. To Lee’s points; I looked at the force graphs on the sight and see that a peek of 100ish lbs was generated, but quickly decayed, (win in 2 sec if I recall correctly). Was this test conducted with the ripcord locked, or was the cable able to move and the piston be ejected from the cylinder? If the piston was moving that would explain the short burst of pressure as the area in the cylinder increases as the piston moves forward, Additionally, I imagine that there is a quick thermal loss, so the gasses contract pretty quick I bet. If the piston was not able to move, then either there was a good about of leakage, or fast cooling of the gasses that resulted in a rapid drop in pressure. As for your legal perspective… I totally agree with you. This might end up being something you just sit back and watch as the manufacturers and riggers blame each other, lol
-
And you would be correct. Basically dead heading the thing, but allowing it to move the cable to see what happens as it completes its stroke.
-
The videos where I see a black ring blowing out of the pin end must have been earlier designs then... Had a thought though that might show how well it is sealed after it fires under load... What if the assembly was submerged in water? Then any escaping gasses would be clearly visible as bubbles.. It would be important to load the pins down so it would require at least 100lbs of pull force to move them. This would allow the internal pressure to reach the upper end of a bent pin or hard pull condition, and show if there is any pressure leakage and from where....Just a thought.. I also sketched up how I would approach this concept... Features would be, that it would be sealed, have a 4 to 6 inch stroke, manually pulling the ripcord would not disturbed the power assist unit, (if that wording makes sense lol) Basically the power assist module would be passive, (i.e., would not be moved even if the ripcord is pulled), until it is pyro activated.. The rip cord would not be fully extractable though when pulled. There would be at least 6 to 8 inches of pull (more than enough to pull the pins up into the housing), but not fully removable when pulled none the less. Oh! and I think it might work with Mr. Booth's new ripcords as well... Unfortunately I have way too much on my plate to build one, but my mind can’t help thinking about this kind of stuff lol… I am curious to see the next episode in the series..