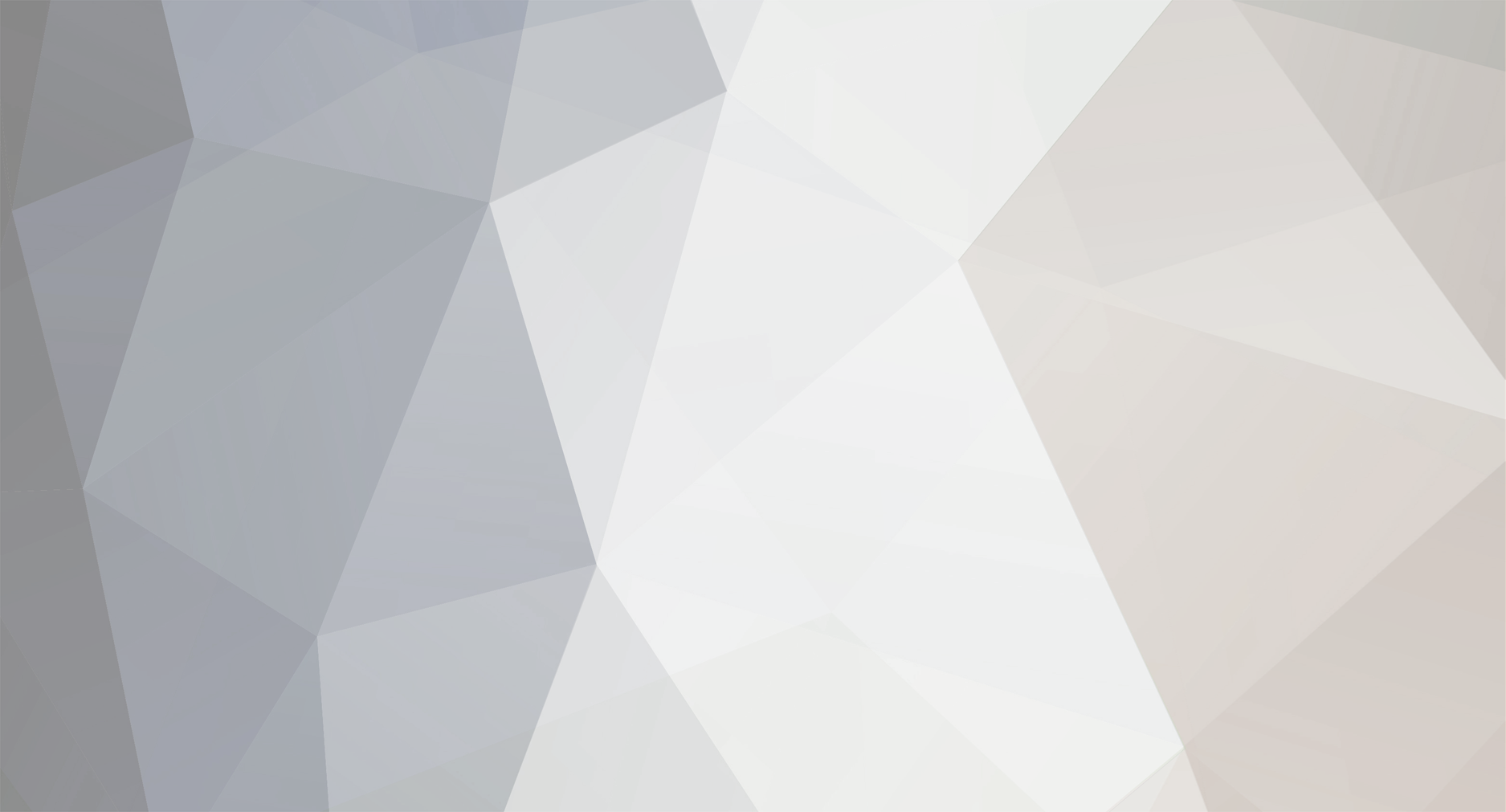
NancyJ
Members-
Content
70 -
Joined
-
Last visited
-
Feedback
0%
Content Type
Profiles
Forums
Calendar
Dropzones
Gear
Articles
Fatalities
Stolen
Indoor
Help
Downloads
Gallery
Blogs
Store
Videos
Classifieds
Everything posted by NancyJ
-
Hey! That's my beautiful Racer Dog!
-
We have a DVD Packing (video) manual that will guide you step-by-step. Call for the $5 DVD and make rigging FUN again! BTW, I use T-Bodkins and our AAD Cutter Threader Tool. The tool is made using a 4 inch long piece of Type 4 (square weave), and (approx.) 16" long piece of 500 lb spectra (Cypres loop material), finger trapped into itself and zigged to the Type 4. See attachment for How To diagram.
-
What deployment method do you have on your primary sport rig?
NancyJ replied to DocPop's topic in Gear and Rigging
I have transitioned dozens of student jumpers from spring-loaded ripcord deployment to pull-out. I like to have my students pull and repack the pull-out 5 to 10 times on the ground. As a result I’ve never failed to have a student land and say, “That was easy… that was fun.” Once they’ve done it correctly once, they always retain the skill. The first lesson to remember is, you don’t throw a pull-out. You PUT the pilotchute where there is no burble, in the fast air beside your head (slightly bent arm, relaxed grip). EASY. I have over 5000 jumps on a pull-out and I‘ve never had a floating handle or any other difficulty with it. Of course I was trained by the best – the inventor of the pull-out, John Sherman. Having made about 100 (springloaded pilotchute) ripcord jumps and over 1200 throw-out jumps I can say without a doubt that the pull-out is easier to use and faster and easier to pack. In the training video “Breakaway”, I was asked to simulate what might happen if the pull-out handle were to somehow get out of its dual end pocket. So in freefall I plucked the handle out of its pocket and let it go. The pull-out handle is attached to a short lanyard that is tucked up under the side flap. When I let go of the pull-out handle, it simply sat there on my butt, sort of leaning against the bottom of the rig. It didn’t float, it didn’t move; it just sat there in my burble. A few moments later I reached back and felt the handle right where I dropped it. From there it was a routine pull and deployment. Upon viewing the footage, the films’ producer and editor dismayed, “That’s not very exciting.” “No, it isn’t”, I said. They were disappointed that the worst scenario malfunction mode of the pull-out was quite benign. The pull-out is so much safer that the throw-out in a number of ways. Neither the pull-out pilotchute or handle are vulnerable, the way the throw-out handle and pilotchute are. The pull-out pilotchute is safely tucked away, inside the container, “where god intended it to be!” The Pull-out is supremely secure for freeflying, sitflying, speed diving, speed style, actually every discipline of skydiving. It effectively makes your rig 2 inches shorter because you don’t have the pouch on the bottom of the container (which is not very attractive to begin with). And you don’t have to replace the BOC pouch when it gets worn and “piccky”. If your container opens prematurely, say from a broken loop, the pilotchute is already out there ahead of the bag. Pull-outs don't sneak their way out of a pouch the way a throw-out can, causing unexpected openings (in the doorway of an aircraft or in freefall). It was a throw-out pilotchute that killed Tom Piras, in just such an accident. It takes about the same force in pounds (if not less), to pull a pull-out pin than it does to pull a throw-out out of its pouch, So there really is no advantage to a throw-out in that regard. With regard to packing, you don’t fold the pc; just flop the pilotchute on top of the bag, stuffing it somewhat into the depression formed by the loop over the top of the bag. Hopefully you’ve packed properly – soft in the middle, firm on the outsides -so that you have a soft area to stuff the pilotchute into. "Why is the throw-out more prevalent than the pull-out?" you may ask. Very simply, aggressive marketing of the throw-out when it first came out. One very prominent instructor from DeLand told me years ago that he thought the pull-out was eminently better (safer), than the throw-out but that in his opinion it was easier to teach the throw-out. He admittedly, was lazy. -
Re: [slotperfect] Manufacturer Contacts On dropzone.com
NancyJ replied to burmite's topic in Gear and Rigging
Technically, if there are broken fibers, you replace the affected portion of the harness (i.e. MLW, legstrap, horizontal, etc.) -
You need to go to the North America Cup Meets. Visit http://styleandaccuracy.wordpress.com/2009-parachute-accuracy-meets/ Contact Cheryl Stearns, Jim Hayhurst, Marius Ivascu for info on more training camps. There's one going on in Lodi, CA right now. Also, Andre Cup Meet at Connecticut Parachutists Inc. Contact Billy Beaudreau.
-
Yes. Aspect ratio and airfoil characteristic ratios remain the same. Apparently, not an easy thing to do. But John Sherman, whiz kid that he is, figured out how to do it.
-
Hi Tim et all, The FireBolt can be a great first purchase if you choose your wing loading wisely. We've had several novice jumpers "jump right into" FireBolts shortly off instruction. Reccommended wing loading for novices is .60 - .90 pounds per sq ft. The FireBolt is a relatively flat trimmed canopy - not a lawn dart. It gets it's long glide, tremendous flare and efficient flight characteristics from the elliptical wing. When lightly loaded the FireBolt is quite docile and forgiving. When heavily loaded, the FireBolt becomes a high performance swooping machine. It is not designed for rear riser landings. It's trimmed rather flat for that to be effective. We're working on a different canopy with that kind of flying in mind... With regard to the dual lower control lines, the brake setting and the concept are really quite simple. There is one brake eye (per side) leading to the outside, upper control lines. Set that brake and stow the excess in the usual fashion according to your riser/toggle setup. On Racer risers we provide a dedicated type III loop on the front of the rear risers through which to route the excess LCL. The excess then loops around the nose of the toggle before it is stowed in the nose keeper. The inside LCL is pushed up to the tail. Only the wingtips are braked. The center of the canopy spills air, softening the opening. The FireBolt is probably the only canopy out there that is truly scaled. From 75 sq ft up to 396 sq ft(Tandem), it is essentially the same canopy. That is what is so ingenious about the FireBolt. Flight characteristics are similar from size to size as long as the wing loading ratio remains the same.
-
If it's been "a few years", you haven't jumped a current production FireBolt. In fact you may have jumped the old Racer TD400 model or the early tapered tip (pre-FireBolt), which were fine canopies for their day. But they were not nearly the fine canopy flying experience that the FireBolt is. I'm told by other users that the FireBolt opens soft like an Icarus - but more orderly, and far outperforms all other current production canopies in terms of flare. Don't salt you food before you taste it.
-
Hi Whoops, You really should investigate the FireBolt Tandem Canopy. It has absolutely the nicest openings - very soft, very smooth. The flare is easy and responsive while the lift is sustained for a long time. There are 3 sizes: 298, 350, 396. The 350 is the best "all around". I like the 298 for the light toggle pressure and sporty feel. At 138 pounds, it works well for me. For some good video of FireBolt openings go to the Jumpshack.com video gallery.
-
Harness comfort is a function of harness geometry and use of the correct material for the task. Proper fit is a must. As a big fellow, distributing your weight in the harness, and not allowing it to point load on the insides of your thighs is even more critical. Start with Type 13 webbing, which is heavier and stronger than Type 7 or Type 8. Then be sure to have a harness where the horizontal portion coming out of the backpad joins the main lift web at a 90-degree angle and becomes the top of the legstrap. The main lift web goes around your butt to become the bottom portion of the legstrap. Look at the attached picture, which shows my own harness. Note that I don't even use legpads, as they are not needed for comfort. I do have some little slide on sheaths in the front to keep the ends of the leg straps from flying in the wind. I do just about every discipline in the sport of skydiving, and wear my harness as you see in the photograph, comfortably - never a bruise. I'll re-emphasize the importance of Type 13, specifically developed as personnel harness webbing, and to be compatible with all harness friction adaptors. Type 7 and Type 8 are both intended for use as cargo netting, and have a tendency to roll at the edge, making it less comfortable, and unsuitable for personnel harnesses. Type 13 won't slip. Type 7 and 8 do slip. In the meantime tighten your harness (legstraps, MLW if adjustable and chest strap), and gut it out.
-
It's not just one factor (the pilotchute being externally mounted for example), that affects speed of reserve deployments. In the case of the Racer, it's the fact that the reserve container opens more freely and completely, has no boxed corners where it counts, has a very bullet-shaped reserve deployment bag, and has a higher drag pilotchute. "Higher that what?" you may ask. Well, in wind tunnel tests, conducted at the NASA Ames Research Facility, the Racer pilotchute demonstrated an 84% drag efficiency. Other pilotchutes that we brought along, and also tested averaged between 40-60%. We used NASA's finely calibrated load cell that was mounted in the tunnel. The Racer pilotchute "stops" better - has greater "snatch" - however you want to say it. It doesn't "slip" through the air as much, in other words. BTW, we happened to be able to conduct these tests in the NASA wind tunnel, because were testing John Sherman's patented variable speed midair refueling drogue that he designed at the bequest of the Marine Corps. The same refuleing drogue can be used to fuel fast flying jets or slow flying helicopters, and still maintain a constant drag. It's quite a remarkable device... But with regard to the speedy reserve deployments, yes the weight of the spring, the type of mesh that's used in the pilotchute, the ease of bag extraction, etc... They all contribute. However, the proof is in the pudding. Go to the Jump Shack website to see repeatable 2-second reserve deployments. It's funny, when Jump Shack first advertised that fact that Racers could consistently produce 2-second reserve deployments, the critics said, "It was irresponsible to advertise such a thing, because it would encourage people to pull low." I'll say it right now - don't pull low.
-
The route cause of leg strap slippage is the webbing selection. The hardware (forged) was originally designed for cotton webbing back in the 40's. Nylon came along and Type 13 (Black edge trace) was designed for use with the existing hardware. Type 13 doesn't slip with unworn personel hardware. Type 7(Yellow edge trace) is cheaper and less strong than Type 13 and it will slip in the original hardware.
-
I forgot to mention the other deficiency of the old style bungee stow/pouch freebag - the destruction of reserve canopies in the event of line strip. There've been several instances where lines tore from reserve canopies, or canopies blew up as a result of line strip. It's not that the canopies were not built strong enough - it's that the deployment system did not meter the lines out in a controlled manner, and sufficiently soften the opening. There has been more than one fatality as a result. Heavy jumpers using small reserves are most susceptible, but jumpers at high altitude DZ's and freeflyers and other "high speed" jumpers are at risk as well. Recent student harness failures are the direct result of line strip openings. People don't realize that the manufacturers of reserve canopies don't do their high speed heavy drops using the old style freebag w/bungee stow & pouch. The canopies wouldn't pass the test (they'd probably blow up or blow thier lines off). All the major manufacturers use "special" bags wherein every stow is a locking stow so that the canopies will take the vicious openings encountered when you static line a 97 sq ft reserve with a 300 pound load at 180 mph! Then those canopies go out into the field where they are assembled into bags that practically guarantee a line dump. Jump Shack was the first company to seriously address the problem. Other companies are beginning to follow suit. The sooner they all do, the better off you'll all be.
-
Keener Rubber Company of Alliance OH makes Mil. Spec. Rubber Bands. They are available from Jump Shack and other manufacturers and dealers. Here are Excerpted Specifications for Mil-PRF-1832E Type I and Type II Parachute bands Type I Mil-PRF-1832E 2 x 1/2 x .032 (MIL-R-1832 Rev D was .040) Type II Mil-PRF-1832E 2 x 3/8 x .062 Table I. Physical Requirements Property Type I Type II Permanent set, percent (maximum) (after 500 +/- 50 percent elongation for 10 minutes) 20 15 Breaking force, pounds (minimum) Initial 45 50 After aging not less than 75% of initial figure Ultimate elongation, percent (minimum) Initial 700 650 After aging not less than 75% of initial figure Weight (minimum), bands/pound 390 300 Flat Length: +/- 1/8 inch Width: Type I +/- 1/16 inch Wall Thickness: +5 percent, -0 percent Table III. Test Methods Characteristic Req. ASTM Requirements Number Results Ref test Applicable to deter- to nearest Method minations Unit Lot per unit Permanent set 3.3 D412 yes one 1 percent Breaking force Lbs./min: Initial 3.3 D412 yes one 1 pound After Aging 3.3 D573 yes one 1 pound Ultimate elongation Percent (minimum) Initial 3.3 D412 yes one 1 percent After Aging 3.3 D573 yes one 1 percent Weight 3.3 yes one 0.1 ounce The old style bungee stow bag with the pouch IS broken, and DOES need fixing. The one case of a canopy being left behind in a container was the result of line dump out of a bag with a POUCH, and only two locking stows. The Speed Bag has 5 to 8 locking stows depending on the size of the canopy. The one case (that I know of) of a freebag that bag locked involved a bag with a BUNGEE STOW that would not break. If there had been rubber bands on that bag - at least one (probably both) would have broken, allowing canopy out of the bag. There is no more potential for bag lock on the Speed Bag than on the old style bungee stow bag that uses a pouch. Some times a canopy will be extracted out of one side of the bag prior to the other side because the canopy will go the path of least resistance. I personally have thousands of jumps on a main Speed Bag and at least a dozen intentional cutaways using a reserve Speed Bag, with no hesitations or locks whatsover. Without a doubt there has been more field testing of the Speedbag than the old style bungee stow freebag, as we have been using the design on main bags for nearly seven years and (tens of) thousands of jumps. For those of you who aren't familiar with pilot rigs, round reserves and parachuting history in general, the sport has been using rubber bands on reserves for 60 or more years, very successfully and reliably. Ask some "old" rigger how a diaper works - ask to see a demonstration of one. The mechanics of the Speed Bag will become more clear to you.
-
looking for racer tandems and student gear
NancyJ replied to skydiverjerry's topic in Gear and Rigging
Call 386-734-5867 New and only slightly used. -
wow!! My Rigger told me I have rubber bands on my reserve bag
NancyJ replied to overmyhead's topic in Gear and Rigging
I have the Mil Spec document that I received from Keener, the manufacturer of Mil Spec Rubber Bands. Jump Shack has sold these rubber bands for as long as I can remember. I will see that it gets posted on the Jump Shack web site, and post it here on Monday. Rubber bands are far superior to the bungee stow for the following reasons. Rubber bands have better retention ability than do the bungee stows. There have been several reserve failures due to line dump/strip that have been attributed to use of the bungee stow, which most riggers don't know or bother to adjust for narrow or wide reserve d-bag. A rubber band will break when it has to (usually between 20 - 40 pounds), thus preventing a bag lock situation. Bungee stows will not break, and are more likely to result in a bag lock on your main or reserve. I have used rubber bands on my own reserve for more than ten years, and would NEVER use a bungee on my last line of defense - my reserve. Mil Spec Rubber bands have been in use longer than the bungee stow has been in existence - some 60 years. We have put rubber bands through the high heat and freeze test during multiple TSO tests. It takes two to three years of extreme temperatures for a Mil Spec rubber band to break down, and frankly, brass has nothing to do with the deterioration. It's a heat and loss of moisture problem. Besides, even if one or more of your rubber bands break on your reserve d-bag, guess what might happen? You might get exactly what you get with virtually every deployment from the old style pouch and bungee reserve bag - a LINE DUMP. For more detailed information read about the Speed Bag (prevents line dump) on the Technical Articles Page at Jumpshack.com. Hope this is helpful. Those who don't know history are destined to repeat it. -
Thus far, I believe the Power Racer is still the smallest container. We haven't made the GA Power Racer (250 cu. in.)in years because when we first made it, it was simply too small for any existing canopies. The bottom line is - send us the smallest canopy you feel safe jumping, we'll throw it in the volume cylinder to get an acurate measurement of it, and then we have the ability to scale the container as small or as LARGE as is required.
-
Actually riggers in the field are not supposed to be manufacturing Reserve Quick Loops, as they are a TSO'd component of the Racer container. You may purchase factory made Quick Loops directly from Jump Shack. The Racer is not difficult to pack. If a rigger tells you that a rig is too difficult for him to pack - it is simply an indication that he hasn't learned how, in which case I would want to seek out a more thoroughly educated rigger. We have trained many riggers (and manufacturers), here at Jump Shack over the years, and I am proud to say we have turned out many of the best. Honestly, I have had apprentice riggers with 4 or 5 packs logged turn out safe, beautiful Racer reserve pack jobs that are better looking than some more "experienced" riggers who simply have not sought out the education.